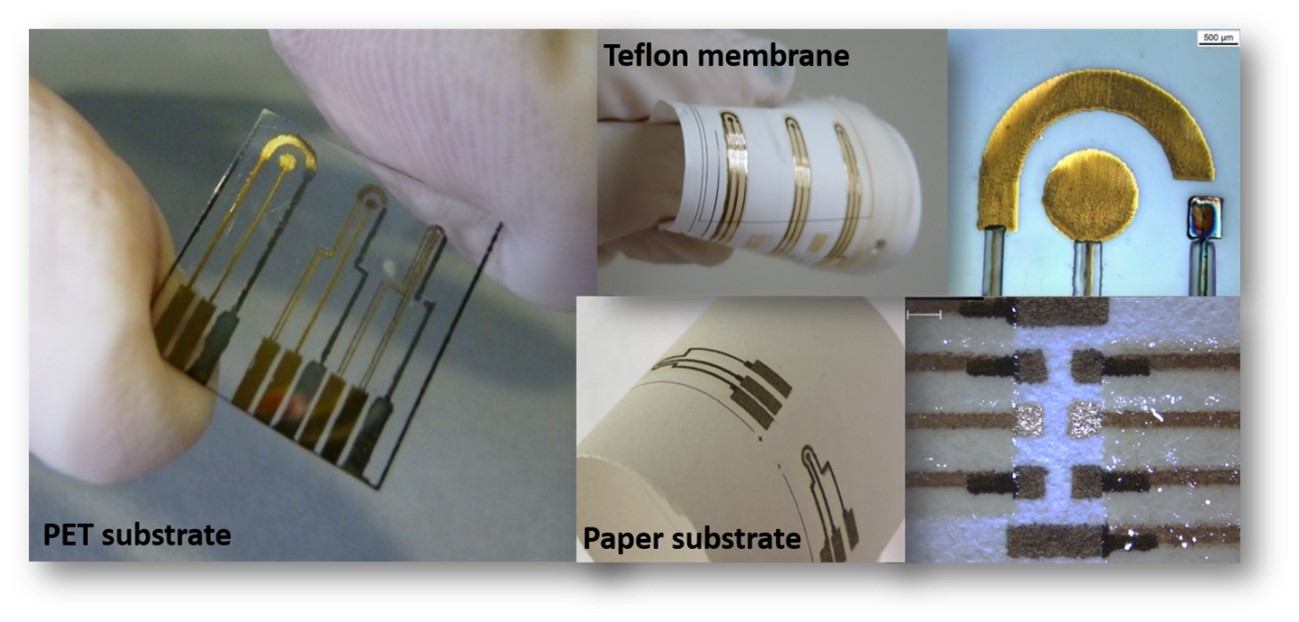
In today’s society there is a great interest in developing new technologies that allow low-cost mass manufacturing, also called “rapid prototyping” or “additive manufacturing”. Rapid prototyping includes technologies such as sterolithography, 3D printing, laser sintering or printed electronics, among others. All of these share digital design and manufacturing from the consecutive addition of layers, that is, techniques that allow creating almost any shape or geometric feature in a very fast time.
Printed electronics consists of printing inks on different types of substrates such as textiles, plastics, papers or films to make them “smart”. This technique is presented as an alternative to traditional silicon that is being implemented in sectors as varied as health and wellness, automotive and transport, professional sports, safety and protection, packaging, architecture and construction, and technical textiles. Printed electronics is one of the new technologies that will have a long history throughout the functional electronic device manufacturing space, with a wide range of applications, electronic designs, processes and materials, compared to conventional electronic and microelectronics based manufacturing technology in silicon. It is expected that in the next decade it will be part of everyday life, with products such as electronic skin, electronic tissues and organs or architectural elements that respond to external stimuli.
Among the many areas of interest of these technologies, one of them is the development of low-cost sensors for the medical or environmental area. For example, in these disciplines, it is essential to get devices that can be very economical or even single-use to promote sustainable environmental control and personalized medicine. Specifically with inkjet technology, researchers from NANBIOSIS Unit 8 Micro-Nano Technology Unit belonging to the Institute of Microelectronics of Barcelona (IMB-CNM, CSIC /and CIBER-BBN), have developed over the last few years multiple materials, inks, substrates and sensors for the development of electrochemical sensors in micrometric dimensions.
- Inks: Most commercial inks are composed of a solvent that contains some material with insulating, conductive or semiconductor properties. As a general rule, an ink must be stable, with a particle size of several orders of magnitude smaller than the injector orifice, have a viscosity of less than 20 mPa s and a surface tension of less than 80 mN m-1. Although these values may depend on the system in question. The final devices are obtained by selectively depositing in previously drawn areas, layer by layer, thin or thick structures on the substrates. They have worked with multiple commercial metallic inks such as gold, silver and platinum.
Normally in an electrochemical system a noble material that is electrochemically stable is needed to be used in the working electrode and in the counter electrode, and for this gold or platinum are a good alternative. To make measurements with any electrochemical sensor, a reference electrode is essential since it is one that has a stable and constant potential over time and that allows us to reference our voltage value. We use the impression of an Ag / AgCl bilayer since it is one of the interfaces most used as a reference electrode. One of the main problems faced by miniaturization, however, is the rapid loss of the small volume of internal reference solution that these electrodes must have, which has a direct impact on their useful life and stability. For this, a polymeric membrane that can be printed was formulated, which allows the reference to have high performance compared to other commercial miniaturized reference electrodes (Ref1). - Substrates: a wide range of rigid, flexible, porous, plastic, fabric, etc. substrates can be used. However, the interaction of the ink with the substrate is crucial in determining the good quality of the printed pattern. For this reason, the properties of the inks are adapted for the different substrates with their own properties. For this reason, it is common practice to pretreat the substrate surface to improve hydrophobicity and adhesion issues mainly. It is common to use plastic substrates with a thickness of the order of microns that provide them with great flexibility and that are already specially treated to obtain excellent printing qualities. The deposition of uniform gold and silver conductive inks on porous substrates can be achieved by using a primer layer to seal the porosity of the membrane in specific and defined areas, with the aim of building a sensor device over the sealed area and leaving the rest of the intact substrate (Ref.2). With a paper substrate, alternatively we can print a silane ink, as a strategy that allows a monolayer of hydrophobic material to grow on the substrate and thus be able to obtain uniform lines of ink on its surface. (Ref.3)
- Sensors developed: Dissolved oxygen (DO) (Ref.4) and pH (Ref.5) sensors have been developed using gold and platinum inks respectively, commercially available on plastic substrates. The inks have a specially designed formulation that allows their sintering at temperatures as low as 150 and 180 ° C for Au and Pt respectively. This is a key point in the development of low-cost sensors made on polymeric substrates or paper that cannot withstand high temperatures. These sensors integrate in a single platform all the basic elements for the registration of pH and DO, allowing measurements without any external electrode. DO is measured directly with a gold working electrode and pH sensors are achieved after electroplating an iridium oxide film on the platinum working electrode. In addition, this water-based platinum ink has another unique feature, it provides the electrode surface with high roughness, which promotes adhesion of the deposited sensor material, in this case iridium oxide. Long-term stability tests for more than 1 year demonstrate excellent stability of the mechanical sensor layer, and that it correlates perfectly with the different roughness of the printed platinum layer. Along the same lines and in relation to the development of inks, it has been possible to obtain a fully printed pH sensor based on a conductive polymer specially formulated to be printed by IJP . The measurements obtained with this ink have a good response in a wide pH range (pH 3 to 10) and the response in the physiological zone (pH 7-7.5) is well resolved, one of the main drawbacks of conductive polymers. We also present an IJP-printed electrochemical sensor for enzyme-free glucose analysis on flexible PEN substrate (Ref.6). In this case, CuO microparticles were used to modify the electrodes, and the detection of glucose was validated in concentrations that coincide with those of the tear fluid, which allows us to foresee applications in ocular diagnosis, where a painless control can be achieved and not invasive of diabetes by analyzing the glucose contained in tears.
(Ref.1): Moya A, Pol R, Martínez-Cuadrado A, Villa R, Gabriel G, Baeza M. Stable Full Inkjet-Printed Solid-State Ag/AgCl Reference Electrode. Analytical Chemistry 91 (2019) 15539-15546
(Ref.2): M. Ortega-Ribera; X. Guimerà; E. Sowade; M. Zea; X. Illa; E. Ramon; R. Villa; J. Gracia-Sancho; G. Gabriel. Online oxygen monitoring using integrated inkjet-printed sensors in a liver-on-a-chip system. Lab on a Chip. 18 – 14, pp. 2023 – 2035. 2018
(Ref.3): All Inkjet Printing Sensor Device on Paper: for Immunosensors Applications M Zea, A Moya, I Abrao-Nemeir, J Gallardo-Gonzalez, N Zine, A Errachid, … 2019 20th International Conference on Solid-State Sensors, Actuators and
(Ref.4): Moya A, Sowade E, del Campo FJ, Mitra KY, Ramon E, Villa R, Baumann RR, Gabriel G. All-inkjet-printed dissolved oxygen sensors on flexible plastic Organic Electronics 39 (2016) 168-176
(Ref.5): Zea M, Moya A, Fritsch M, Ramon E, Villa R, Gabriel G Enhanced performance stability of iridium oxide based pH sensors fabricated on rough inkjet-printed platinum ACS Applied Materials & Interfaces 11 (2019) 15160-15169
(Ref.6): Romeo A, Moya A, Leung TS, Gabriel G, Villa R, Sánchez S. Inkjet printed flexible non-enzymatic glucose sensor for tear fluid analysis Applied Materials Today 10 (2018) 133-141