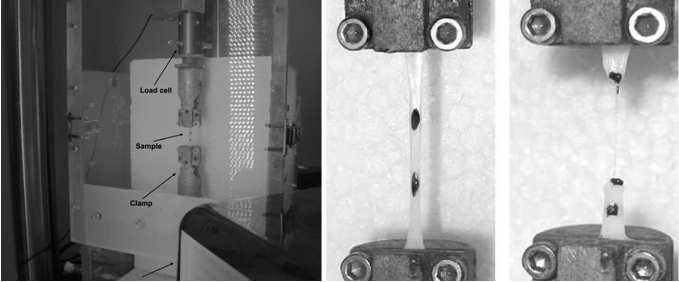
The experimental study of the mechanical properties of biological tissues is of vital importance. Thorough research into themechanical response of biomaterials is the basis for the creation ofmodels which can accurately reproduce the mechanical behavior ofsuch materials. Adequate mechanical characterization of tissue materials is of paramount interest to the clinical simulations, diagnostic and tissue engineering fields – where the tissue structure, in contrast to classical mechanics application fields, is just simply a biological tissue.
In order to obtain their material properties, classical engineering testing techniques have been applied to biologicalmaterials. To reproduce the mechanical behavior of these kinds ofmaterial, many constitutive models have been proposed for softtissues (. In some cases, the validation of these models basedon only uniaxial test data is inappropriate because biological andbiomaterial membranes generally develop multiaxial stress statesduring real-life loading conditions.Although a large number of experiments have been conductedover the years on measuring the structural and functional properties of biological tissues, the standardization of such measurementsand the interpretation of results are difficult to establish. The geometry of the sample, the method of gripping the sample edges andthe method used to determine the strain may have profound effectson any measured mechanical properties since they directly influence how the load is transferred to the membrane.
In typical (hard) engineering materials like metals and composites, strain may be measuredat any instance during the mechanical test. Some techniques require a close contact with the samplesduring the test. The use of extensometers attached directly (glued with cyanoacrylateadhesives, for instance) to the gage section of the test specimen, and strain gages thatare mounted directly to the specimen. Sincestrain gages have knife edges to define the exact points of contact with the specimenthey are also incompatible with soft tissues.Imaging techniques such as video extensometry or digital image correlation may be an alternative to the contact methods. Digitalimage correlation (DIC) is based on a process called imagematching. It is possible to use this technique to measure surface displacement and buildup full field 2D and 3D deformation vector fields and in-plane strain maps. It requiresa set of markings, known as speckle, on the analyzed surface(s).Video extensometers performing principle is based on tracking i.e., on following theposition of a given number of markings or regions of interest (ROI).
For the particular case of tension tests (uniaxial or biaxial), the physical quantitiesdirectly measurable are the load, F and the elongation, l.These quantities are normalizedto account for the test specimen’sgeometry. The normalizedengineering parameters arethe engineering stress, σ and engineering strain or stretch λ. Engineeringstress is the ratio between theload F and the sample’s crosssection i.e., σ = F/A. Engineeringstrain is given by=l/lo and engineering stretch λ=1+.
Creep and relaxation tests are sometimes performed to determine the viscoelastic properties ofsoft tissues; specimen deformation is measured under a constant force in creep testing, whereasin relaxation tests, change in load is determined under constant specimen length. In these tests,stress (= load divided by undeformed specimen cross-sectional area) and strain (= change inspecimen length divided by reference length) are commonly used to represent the data.